
Testing/ Results
Construction Testing
One of the key features for designing an ergonomically friendly pruner housing was designing it in a way that it could be assembled quickly. The goal of the design was to be able to assemble the pruner in less than 6 minutes. On the left you can see the construction steps used when assembling the pruner.
CONTROL
The control of the experiment was that three individuals who had never assembled the pruner before were tested. Their only instructions were to assemble it as quickly as possible and given the required tools as long as the construction steps.
DISCUSSION
This experiment was accurate to real world construction scenarios. The pruner came disassembled in its four basic parts, the drive shaft, the housing, the cutter, and the motor.
RESULTS
As you can see in the graph above, all three individuals beat the anticipated construction time with an average of 7.2% faster than the goal.
Step 1: Organize all for parts that will need to be put together, the drive train assembly, the central housing, the cutter system and the Makita power drill.
Step 2: Assemble the blade linkages to the end of the drive shaft with the 1/4” flat head pin.
Step 3: Lock the drive shaft to the Makita power drill by using the self-locking pin.
Step 4: Slid the central/motor housing over the dive shaft and screw the motor housing onto the Makita power drill.
Step 5: Slide on the cutter assembly, first attach to the central housing by sliding the support pin through the inside of the central housing and bolt the support pin on from outside of the cutter assembly. Then attach the linkages to the blade using another ¼” flat head pin.
Step 6: Test that the pruner has been successfully assembled by slowly giving power to the power drill. If the blades move you know that the pruner was assembled correctly.

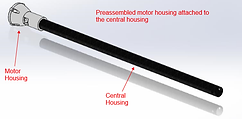
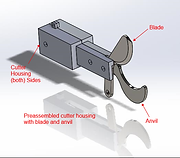


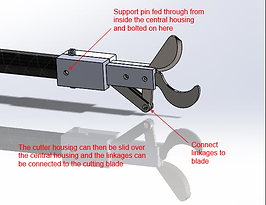
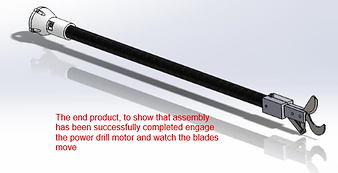

SUMMARY OF TESTING
The remainder of the tests preformed on the pruner housing were measured in a pass/fail system. With this portion of the pruner project, there were many design restrictions. In the following table the results of each individual test is evaluated.
While not every test was a success, the new pruner housing design was an improvement and with an increase of overall strength the pruner housing is sure to be a complete success in the future.
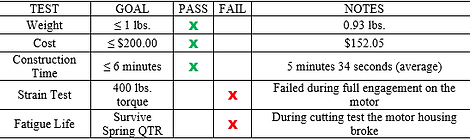
Results
Results from testing
During the strain gage there were some complications about how well the pruner was running. First the concentricity of the drive shaft was out of tolerance causing the whole pruner to jar up and down. Secondly, the stresses caused on the motor housing were not all rotational as expected. There was a jarring radial load that caused a lot of fatigue on the motor housing. After testing the pruners cutting capabilities, the motor housing sheared off at the base on the half inch branch cut test. The cause of the failure was due to fatigue loading and also the torsional shear stress, the slight radial load applied to the motor housing form the misaligned drive shaft caused the failure in the motor housing.
Potential Solutions to the Housing
In order to fix the motor housing in the future, the three points of concern can be addressed. The housing material can be re-evaluated. Obviously, ABS plastic does not have a high grade strength. Therefore by using a high strength aluminum housing the motor housing would be better at withstanding the stress loads applied to it. The last easy solution in strengthening the overall pruner housing is to build a cutter housing out of a single piece of aluminum stock, this would prevent a lot of concentric and symmetric tolerances being put into place but also take away the need to rely on a fastening screw that has to withstand all of the stress loads.
General Cutting Test
ORIGINAL MOTOR HOUSING
-Cutting test failed at 0.5" on second attempt
-Leading cause of failure was torsional shear stress and fatigue loading exerted onto the motor housing.
EXTRA SUPPORTED HOUSING
-Cut several branches at both 0.5" and 0.75" with no visible signs of deformation or fatigue.
-Testing stopped before source so the pruner could be presented.
-Accidental drop after source terminated further testing
-Maximum cutting capability still unknown.